Practical Approaches to Lower Manufacturing Waste
In the expanding global market, manufacturing companies face the dual challenge of increasing productivity while
minimizing waste. Not only does reducing
manufacturing waste enhance environmental sustainability, but it also significantly cuts costs and improves operational efficiency. This article will delve into effective strategies to lower waste in manufacturing processes, offering valuable insights for businesses aiming to optimize their production lines.
Understanding the Types of Manufacturing Waste
Before exploring the methods to reduce waste, it's essential to understand the various types of waste in manufacturing processes. Typically, manufacturing waste can be classified into several categories:
- Defects: Products that don't meet quality standards and require rework or disposal.
- Overproduction: Producing more than what is required, leading to excessive inventory that ties up resources.
- Waiting: Idle time when resources are not being efficiently utilized.
- Non-Optimized Processing: Using more resources or steps than necessary to complete a task.
- Unnecessary Transport: Excess handling and movement of materials that do not add value.
- Inventory: Excess products or materials that are not needed immediately.
- Motion: Unnecessary movements of people or machines that do not add value to the product.
- Underutilized Talent: Not making full use of employees' skills and talents.
Implementing Lean Manufacturing Techniques
One of the most popular strategies for reducing manufacturing waste is the adoption of
Lean Manufacturing principles. Lean focuses on streamlining operations, improving process efficiency, and maximizing value by eliminating waste. Key Lean practices include:
- Kaizen: A continuous improvement strategy that encourages all employees to contribute to refining processes and reducing waste.
- 5S Methodology: A system of workplace organization aimed at enhancing efficiency and effectiveness. It includes Sort, Set in order, Shine, Standardize, and Sustain.
- Value Stream Mapping: Analyzing and designing the flow of materials and information to reduce waste and improve process efficiency.
- Just-in-Time (JIT): Producing only what is needed, when it is needed, and in the exact amount, reducing excess inventory and production waste.
Utilizing Technology for Waste Reduction
The integration of advanced technology in manufacturing processes can substantially lower waste. Key technological advancements that can assist in waste reduction include:
- Automation and Robotics: Automation reduces human error and increases precision, leading to lower defect rates and material waste.
- IoT and Data Analytics: Utilizing the Internet of Things (IoT) and data analytics to monitor operations in real-time helps identify waste patterns and implement timely corrective measures.
- 3D Printing: Additive manufacturing techniques like 3D printing allow for precise material usage, minimizing excess material waste.
Adopting an Eco-Friendly Approach
Sustainable practices not only lower manufacturing waste but also improve brand reputation and ensure compliance with environmental regulations. Consider incorporating the following eco-friendly practices:
- Recycling and Reusing: Establish systems to recycle and reuse materials within production processes.
- Energy Efficiency: Implementing energy-efficient equipment and practices to reduce energy wastage.
- Waste Segregation: Segregating waste to facilitate better recycling and disposal processes.
Encouraging Employee Involvement
Employee involvement is critical in efforts to reduce waste in manufacturing processes. Engaged employees are more likely to suggest improvements and contribute to waste reduction initiatives. Strategies include:
- Training Programs: Provide continuous training to employees about waste reduction techniques and the importance of sustainable practices.
- Incentive Systems: Develop rewards for employees who suggest effective waste reduction ideas.
- Communication Channels: Establish open communication channels for employees to share feedback and recommendations.
Regular Monitoring and Evaluation
Regular monitoring and evaluation of manufacturing processes is vital for identifying waste generation points and measuring the effectiveness of waste reduction strategies. Consider the following:
- Key Performance Indicators (KPIs): Establish KPIs to actively measure waste production and reduction goals.
- Periodic Audits: Conduct regular audits to ensure compliance with waste reduction targets and identify areas for improvement.
- Continuous Feedback Loop: Create a loop for continuous feedback to quickly address inefficiencies or problems as they arise.
Conclusion
Reducing waste in manufacturing is not just an environmental concern; it is a crucial component of achieving operational excellence. By leveraging
Lean manufacturing principles, adopting modern technologies, fostering a culture of sustainability, engaging employees, and continuously monitoring processes, manufacturers can significantly cut down on waste and boost profitability. Embracing these practices will not only lead to a more sustainable future but also ensure a competitive edge in an increasingly conscientious market. Lowering manufacturing waste is a journey, but with strategic planning and execution, notable improvements can be achieved.
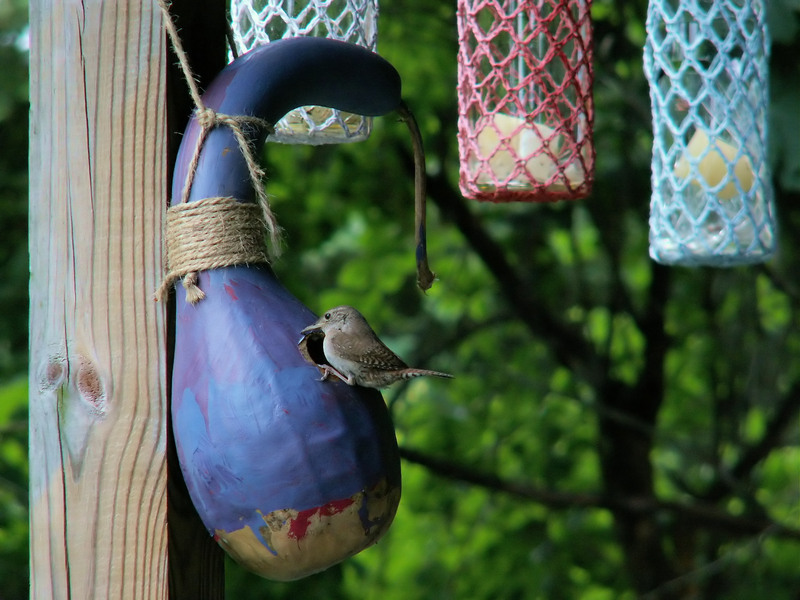
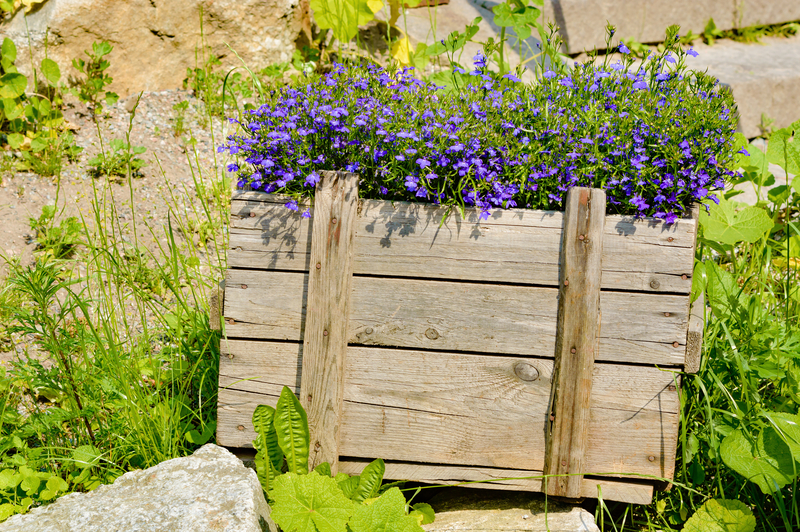